Vinyl records, also known simply as records, are analog sound storage mediums made from polyvinyl chloride (PVC). First introduced in the late 19th century, they became the primary format for music consumption through much of the 20th century. With their distinctive grooves and the iconic crackle that accompanies playback, vinyl records offer a unique listening experience cherished by audiophiles and music enthusiasts alike. Despite the advent of digital music, vinyl has seen a significant resurgence in recent years, celebrated for its warm sound and tangible connection to music history.
This article aims to demystify the fascinating process behind how vinyl records work. By exploring the history, anatomy, recording, and playback mechanisms, we’ll uncover the intricate science and art that bring these analog treasures to life. Whether you’re a seasoned collector or a curious newcomer, this comprehensive guide will enhance your appreciation of vinyl records and their enduring appeal.
History of Vinyl Records
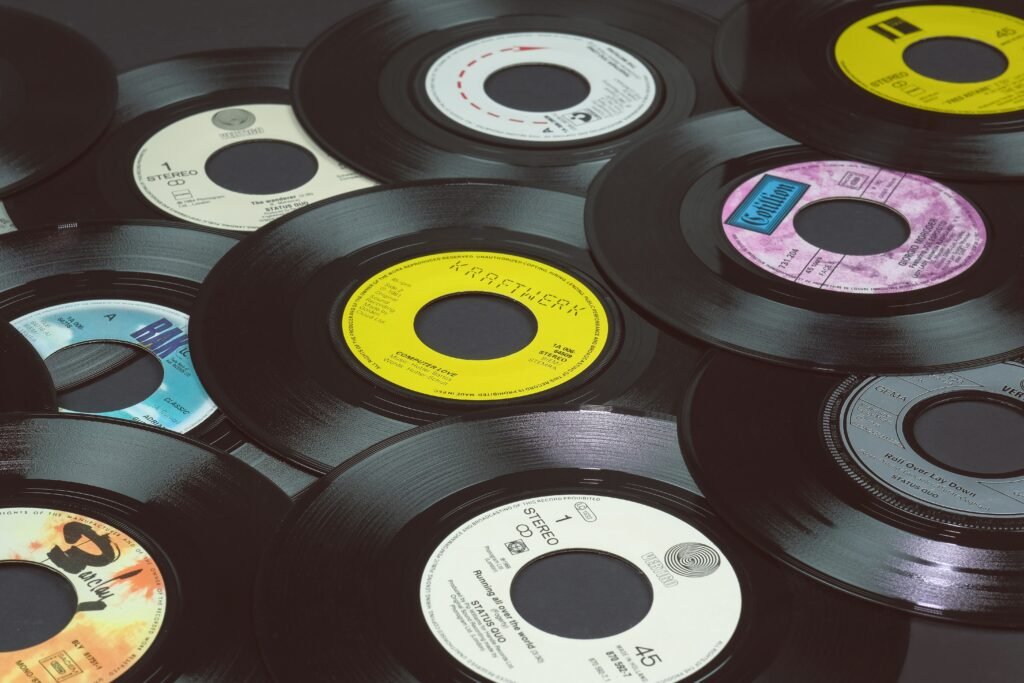
Origins and Evolution
The journey of vinyl records begins in the late 19th century with the invention of the phonograph by Thomas Edison in 1877. Edison’s early phonographs used cylinders wrapped in tin foil to record and reproduce sound. Shortly after, Emile Berliner introduced the flat disc record in the 1880s, which became the foundation of the modern vinyl record. These early records were made from hard rubber and shellac, a brittle material that dominated the market for decades.
In the 1940s, advancements in materials led to the development of polyvinyl chloride (PVC) records, or “vinyl” as they are commonly known. Vinyl offered improved durability, flexibility, and sound quality compared to shellac. This shift set the stage for the golden age of vinyl records, which began in the 1950s.
Key Milestones in Development
1948: Introduction of the LP (Long Play) Record
Columbia Records revolutionized the industry with the 33⅓ RPM LP, allowing up to 22 minutes of music per side. This format became standard for albums.
1949: Emergence of the 45 RPM Single
RCA Victor introduced the 45 RPM single, designed for shorter recordings like singles and EPs (extended plays). This format became popular for jukeboxes and radio play.
1957: Stereo Sound Recording
The development of stereo sound recording, which allowed for two-channel audio, added depth and dimension to vinyl playback. This innovation enhanced the listening experience and became widely adopted in the 1960s.
1970s: Peak Popularity
The 1970s marked the peak of vinyl records, with album sales reaching unprecedented levels. Iconic records from this era are still celebrated today.
1980s: Decline and the Rise of Digital
The advent of the compact disc (CD) in the early 1980s began to overshadow vinyl records. CDs offered portability and digital clarity, leading to a significant decline in vinyl sales.
2000s-Present: Vinyl Revival
Despite a period of dormancy, vinyl experienced a resurgence in the 2000s. Audiophiles, collectors, and new generations of listeners were drawn to its tactile and auditory appeal. Vinyl sales have continued to grow, driven by a renewed appreciation for analog sound and physical media.
Anatomy of a Vinyl Record
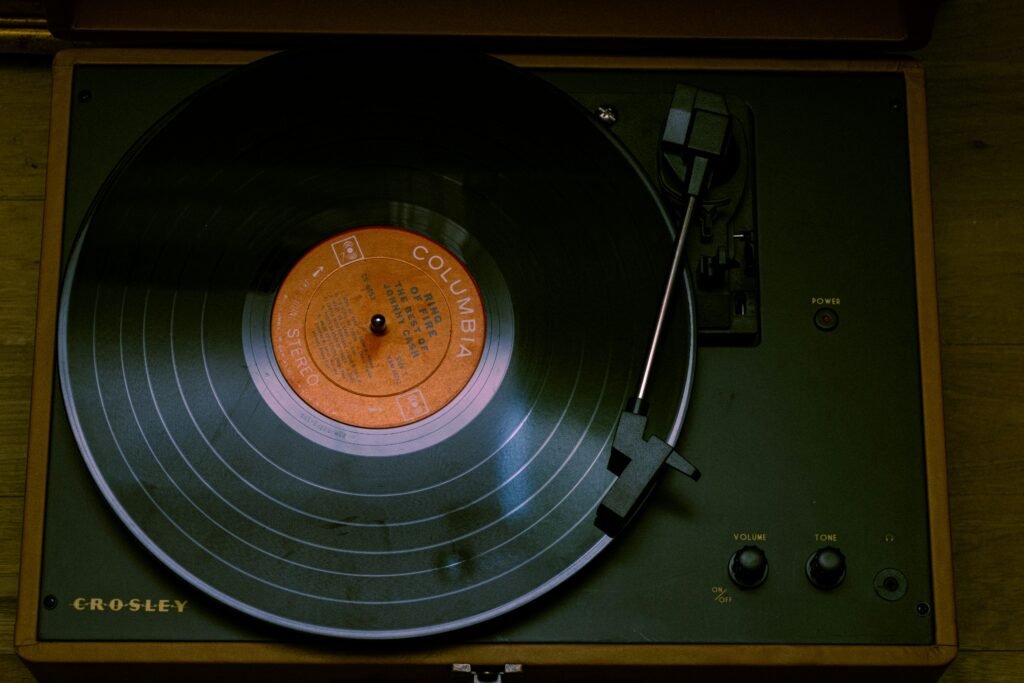
Physical Components
Grooves:
The most crucial part of a vinyl record is the spiral groove that starts near the edge and ends near the center. This groove is meticulously cut into the vinyl surface and contains the analog representation of the sound. Variations in the groove’s width and depth encode the audio information, which is read by the stylus during playback.
Labels:
The label is the central, flat part of the record that does not contain grooves. It usually displays information about the record, such as the artist, album title, track list, and record company. The label helps to identify the record and provides essential details to the listener.
Ridges and Run-Out Area:
Between the grooves and the label, there are often ridges or land areas that help stabilize the stylus before and after it plays the music. The run-out area is a blank section near the center where the groove spirals tightly, often containing inscriptions or hidden messages from the artist or producer.
Outer Edge:
The outermost part of the record is often slightly raised to protect the grooves from damage when handling or placing the record on a flat surface.
Different Sizes and Speeds
33⅓ RPM (LP – Long Play)
Size: Typically 12 inches in diameter.
Speed: 33⅓ revolutions per minute.
Use: Primarily used for full-length albums, allowing up to 22 minutes of audio per side. The slower speed and larger size accommodate more grooves and thus more music.
45 RPM (Single)
Size: Typically 7 inches in diameter.
Speed: 45 revolutions per minute.
Use: Commonly used for singles and extended plays (EPs). These records usually contain one or two tracks per side and are known for their higher fidelity due to the faster rotation speed.
78 RPM
Size: Usually 10 inches in diameter (but can vary).
Speed: 78 revolutions per minute.
Use: The standard format for records produced before the 1950s. These records have shorter playtimes, typically around 3-4 minutes per side, and are made from shellac rather than vinyl, making them more brittle and prone to breakage.
The Recording Process
How Sound is Recorded onto Vinyl
Recording sound onto vinyl is a meticulous process that transforms audio waves into physical grooves on a record. It involves several stages to ensure high-fidelity reproduction of the original sound:
Audio Source:
The process begins with the audio source, which can be live music or pre-recorded tracks. These sounds are captured using microphones and mixed in a recording studio to create the final audio mix.
Mastering:
The mixed audio is then transferred to a mastering engineer, who prepares the audio for vinyl. This stage involves equalizing the sound, compressing dynamic ranges, and adjusting the overall volume to ensure optimal playback quality on vinyl. The final mastered audio is then ready for the cutting process.
Cutting the Master Disc:
The mastered audio is sent to a cutting lathe, a precision machine used to engrave the audio signal onto a master disc. The lathe converts the electrical audio signals into mechanical movements. A cutting stylus, which is a diamond-tipped tool, vibrates in response to these signals and carves the grooves into the surface of the master disc, which is usually made of lacquer-coated aluminum.
Role of the Master Disc and Cutting Lathe
Master Disc:
The master disc, or lacquer master, is the first physical representation of the final audio on vinyl. It serves as the template for all subsequent copies of the record. The quality and precision of the master disc are crucial, as any imperfections will be replicated in all produced records.
Cutting Lathe:
The cutting lathe is a specialized machine essential for creating the master disc. It has two primary components:
Cutter Head: Contains the cutting stylus that etches the audio signal into the lacquer surface. The cutter head moves across the surface of the master disc, guided by the audio signal.
Turntable: Rotates the master disc at a consistent speed, typically 33⅓ or 45 RPM, allowing the cutter head to engrave the continuous spiral groove that captures the sound.
Electroplating and Mother Disc
After the master disc is cut, it undergoes an electroplating process to create a metal stamper. This stamper is used to press the grooves into the vinyl during manufacturing. The electroplating process involves coating the lacquer master with a thin layer of silver, followed by a nickel bath that hardens into a negative image of the grooves. This negative is known as the “father.” From the father, a “mother” disc (positive image) is created, which can then produce multiple stampers (negatives) for pressing records.
Pressing Vinyl Records
The final step involves using the stampers to press the audio grooves into vinyl discs. The vinyl material is heated and pressed between the stampers, embedding the grooves into the surface. After cooling, the excess vinyl is trimmed, and the finished records are inspected for quality before packaging.
The Playback Mechanism
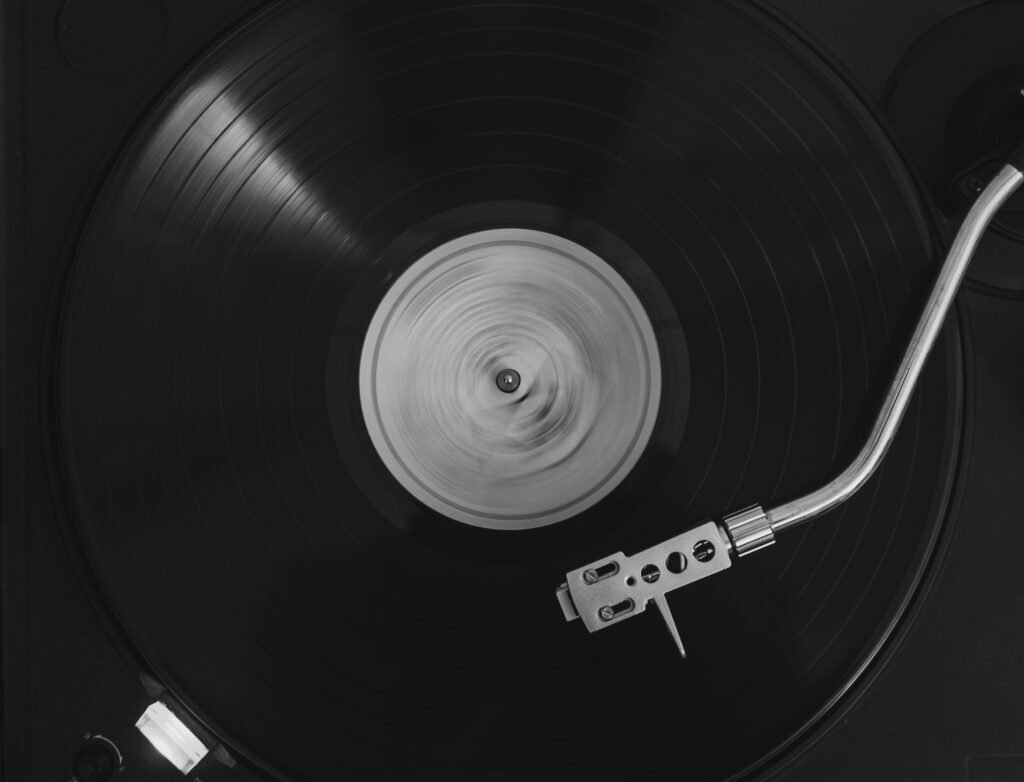
Turntable Components
Platter:
The platter is the rotating platform on which the vinyl record sits. It is designed to spin at a consistent speed (typically 33⅓, 45, or 78 RPM) to ensure accurate playback. High-quality platters are often made of materials like aluminum or acrylic to minimize vibrations and provide stable rotation.
Tonearm:
The tonearm holds the cartridge and stylus and guides them across the record’s surface. It is balanced to ensure the stylus tracks the grooves accurately without exerting excessive force that could damage the record. Tonearms can be straight or S-shaped and often feature counterweights and anti-skate mechanisms to maintain proper alignment and pressure.
Cartridge:
The cartridge is mounted at the end of the tonearm and houses the stylus. It contains a cantilever and magnets or coils that convert the stylus’s movements into electrical signals. Cartridges come in various types, including moving magnet (MM) and moving coil (MC), each offering different levels of fidelity and performance.
Stylus:
The stylus, or needle, is the tiny, diamond-tipped component that makes direct contact with the record’s grooves. As the record spins, the stylus traces the grooves’ undulations, picking up the encoded audio information. The shape and quality of the stylus are crucial for accurate sound reproduction and minimizing wear on the record.
How the Stylus Reads the Grooves
The grooves on a vinyl record are not uniform; they vary in width and depth to represent the audio signal. As the stylus travels along these grooves, it vibrates in response to the undulations. These vibrations correspond to the original sound waves that were recorded onto the vinyl. The stylus’s precise tracking of these variations is essential for faithful playback of the recorded audio.
Conversion of Mechanical Vibrations to Electrical Signals
The playback process involves converting the mechanical movements of the stylus into electrical signals, which can then be amplified and played through speakers:
Vibrations to Electrical Signals:
As the stylus moves along the grooves, it causes the cantilever within the cartridge to vibrate. In a moving magnet (MM) cartridge, these vibrations move magnets near coils of wire, inducing an electrical current. In a moving coil (MC) cartridge, the coils themselves move within a magnetic field, generating the electrical signal directly.
Signal Transmission:
The generated electrical signals are very weak and need to be transmitted through the tonearm wires to the turntable’s output terminals. From there, they are sent to a phono preamp.
Phono Preamp:
The phono preamp amplifies the weak signals from the cartridge to line level, making them suitable for input into a standard amplifier or receiver. The preamp also applies the RIAA equalization curve, which corrects the frequency response to ensure accurate sound reproduction.
Amplification and Playback:
The amplified signals are then sent to the main amplifier, which drives the speakers. The speakers convert the electrical signals back into sound waves, allowing listeners to hear the music as it was originally recorded.
Sound Reproduction
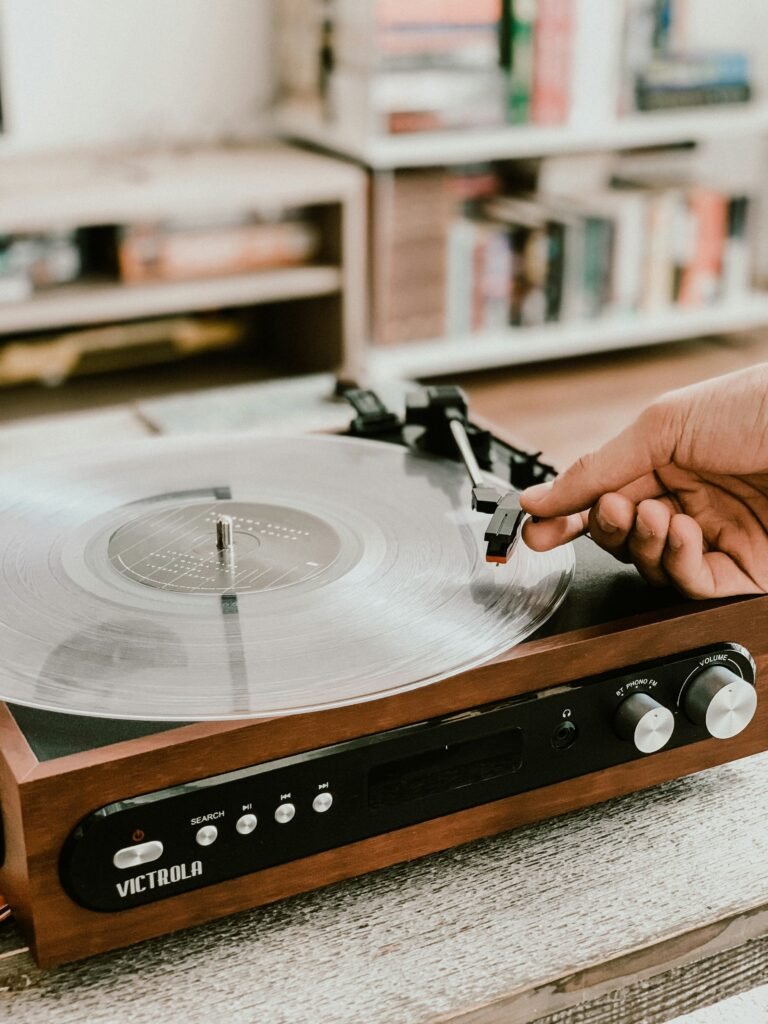
Amplification and Speakers
The journey from the grooves of a vinyl record to the sound heard by the listener involves several critical steps of amplification and sound reproduction:
Amplification:
After the phono preamp boosts the signal from the turntable’s cartridge and applies the necessary equalization, the signal is sent to a power amplifier. This amplifier increases the signal’s strength to a level that can drive the speakers effectively. Modern amplifiers can be integrated units that include both preamp and power amplification stages or separate components for dedicated performance.
Speakers:
The amplified signal reaches the speakers, which convert the electrical energy back into mechanical energy, creating sound waves. Speakers consist of drivers (woofers, tweeters, and sometimes mid-range speakers) that handle different frequency ranges. High-quality speakers ensure that the sound reproduction is accurate and that the nuances of the vinyl recording are faithfully delivered to the listener.
Factors Affecting Sound Quality
Several factors influence the sound quality of vinyl playback. Proper maintenance and care of both the vinyl records and the playback equipment are essential for optimal performance:
Stylus Condition
The stylus (needle) is the first point of contact with the record’s grooves. A worn or damaged stylus can mistrack the grooves, leading to distorted sound and potential damage to the record. Regular inspection and timely replacement of the stylus are crucial for maintaining sound quality.
Record Wear
Vinyl records are susceptible to wear and tear from repeated play. Scratches, dust, and dirt can accumulate in the grooves, causing pops, clicks, and other unwanted noises. Proper cleaning and handling of records can minimize wear and prolong their lifespan.
Turntable Setup
The alignment and calibration of the turntable components significantly impact sound quality. This includes setting the correct tracking force, anti-skate adjustment, and ensuring the tonearm is balanced. An improperly set up turntable can cause tracking errors and uneven wear on records.
Environmental Factors
The environment in which the turntable operates can affect performance. Vibrations from external sources, such as footsteps or speakers, can cause the stylus to skip or mistrack. Placing the turntable on a stable, vibration-free surface helps mitigate these issues.
Quality of Components
The quality of the turntable, cartridge, tonearm, and even the phono preamp and amplifier can all influence sound reproduction. Investing in high-quality components often results in better sound fidelity and an enhanced listening experience.
Speaker Placement and Room Acoustics
The positioning of speakers within a room and the room’s acoustic properties play a crucial role in sound quality. Proper speaker placement and addressing acoustic issues (such as reflections and absorbent surfaces) can improve clarity, imaging, and overall sound reproduction.
Cleaning and Maintenance
Regular maintenance of both the vinyl records and the playback equipment ensures longevity and consistent sound quality. Cleaning records with appropriate brushes and solutions, as well as keeping the stylus and turntable components dust-free, are essential practices for any vinyl enthusiast.
Closing Thoughts
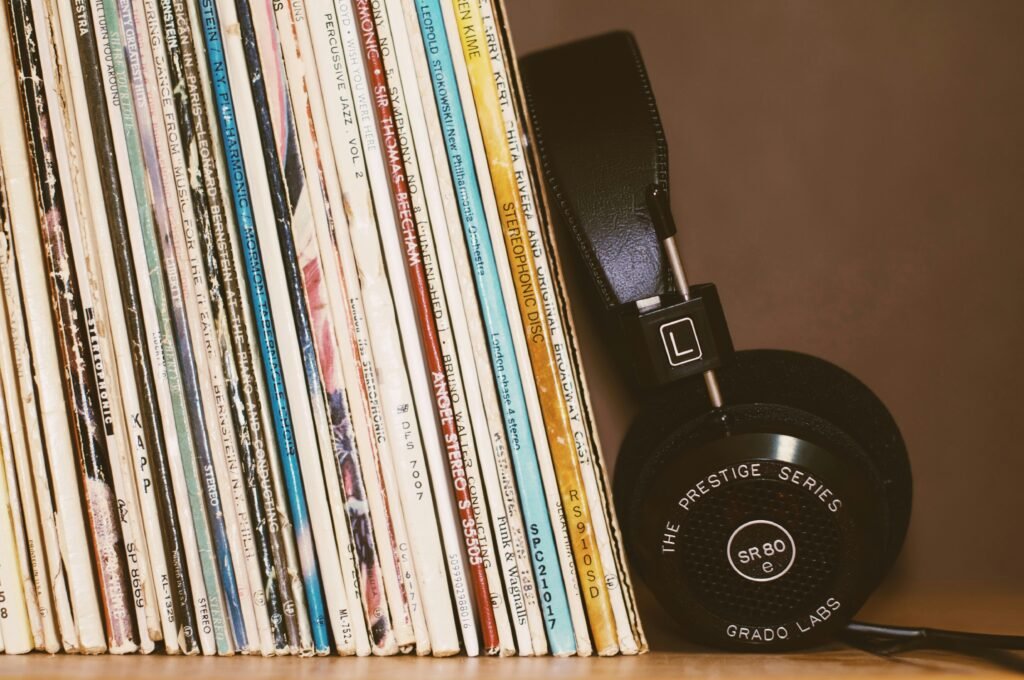
Vinyl records, a timeless medium for music storage and playback, have a rich history that dates back to the late 19th century. They evolved from Edison’s phonograph cylinders to Berliner’s flat discs, ultimately transitioning to durable vinyl in the 1940s. Key milestones such as the introduction of the 33⅓ RPM LP, the 45 RPM single, and the advent of stereo sound significantly shaped the vinyl landscape.
The anatomy of a vinyl record, including its grooves, labels, and various sizes and speeds, is essential for understanding how music is physically encoded and read. The recording process involves transferring audio to a master disc using a cutting lathe, followed by pressing the vinyl copies. During playback, the turntable’s components—platter, tonearm, cartridge, and stylus—work in harmony to convert the grooves’ physical undulations into electrical signals, which are then amplified and reproduced as sound through speakers.
Sound reproduction quality is influenced by several factors, including the condition of the stylus and records, the setup of the turntable, environmental conditions, and the quality of audio components. Proper maintenance and careful handling are crucial to preserving the integrity and performance of vinyl records.
Enduring Appeal of Vinyl Records
The enduring appeal of vinyl records lies in their unique combination of tactile, visual, and auditory experiences. The physical act of handling a record, admiring its cover art, and carefully placing the stylus onto the grooves creates a ritualistic connection to the music. Vinyl’s analog sound, often described as warmer and richer than digital formats, offers a distinct listening experience that many audiophiles and music enthusiasts prefer.
In an age dominated by digital music, the resurgence of vinyl underscores a desire for authenticity and a deeper engagement with music. Collectors appreciate the tangible nature of vinyl, the nuances of sound that only analog can provide, and the historical significance of owning a piece of music history. Vinyl records are not just about listening to music; they represent an art form and a cultural artifact that continues to captivate generations of listeners.